This is my home made monotube coil winder. It has been used to wind pancake coils (as it is doing here) and helical coils and frusto-conical coils and the kind of wide spaced helical coils that are used for Ofeldt boilers. Here it is shown winding half inch schedule 40 black iron with welded seam. This is good enough as it has an 8,000 psi burst strength. We have wound everything from ¼” to ½” 316 Stainless to 1” schedule 80 black iron. |
|
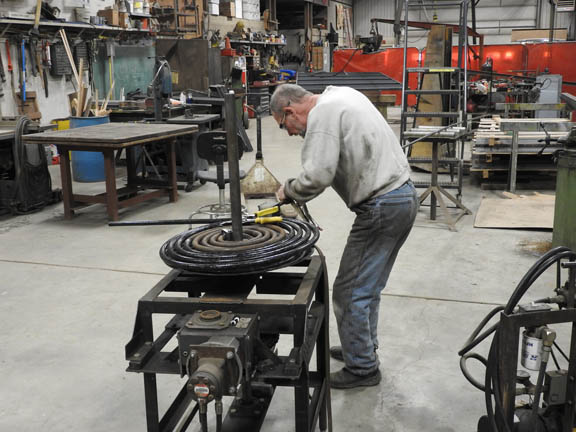 |
|
|
|
|
(Note: Click on a picture to see a larger view and then use your browser to enlarge it further.) |
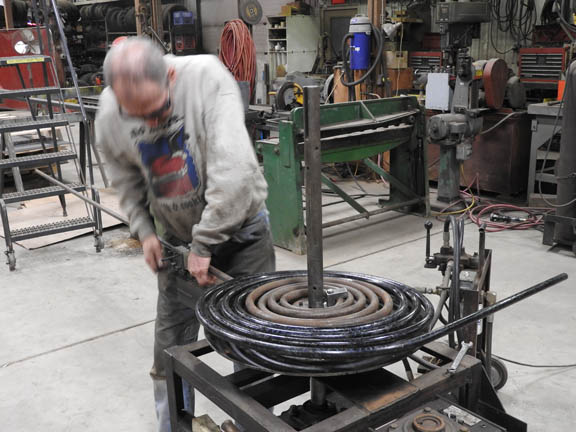 |
|
Usually we take a standard 21’ length of black iron pipe and make it into an 18” diameter pancake coil. Today we are taking three lengths of standard 21’ black iron, butt-welding them end to end and winding a double pancake coil 22” in diameter. The beauty of this system is that one does not need to do a weld in the center. That is very difficult to do and involves a lot of heating with a torch and beating around and trimming with a cutoff saw. It is not easy to work in the center small space and do a good weld. When winding a coil it always takes one or two tries to get things sorted out as we forget some of the details over the intervening years. Here we are fighting with the bottom coil as the windings are trying to climb over each other. We have solved this technical problem later on. |
|
|
|