Electronic Controls:
An absolute shaft encoder measures the angle of crankshaft rotation; a control circuit (logic circuit or a microprocessor) derives the position of the piston in the cylinder, and also the engine RPM. When the piston reaches TDC, the intake valve is forced open by the piston; immediately thereafter, the control circuit activates the solenoid to keep the intake valve open to allow steam to enter the cylinder. When the control circuit switches off the current to the solenoid coil, the intake valve closes (steam cutoff). For example, as the load increases on the steam engine, the control circuit can hold the intake valve open for a longer period during the power stroke (letting in more steam), and thus maintain constant RPM. Other control modes for variable speed or power are possible. |
Design Details:
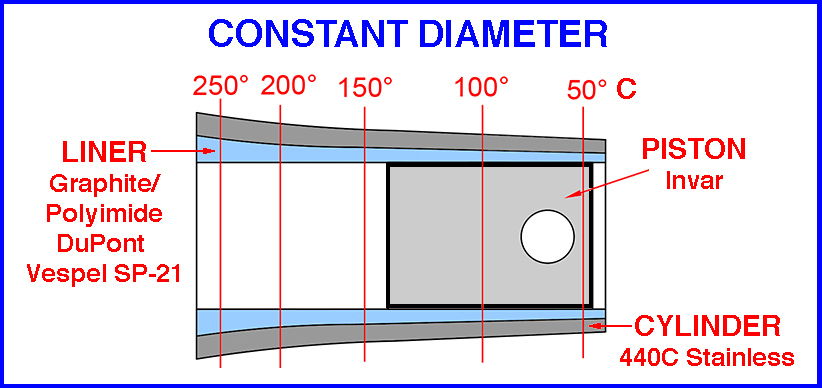
Constant Diameter Cylinder and Piston (The diameter change with temperature is highly exaggerated for clarity.)
The cylinder of a uniflow steam engine has large temperature gradient along its length, since – in order to maintain efficiency – it cannot be cooled (unlike a water-cooled IC engine). The hot end of the cylinder will have a larger diameter than the cooler exhaust end. However, an “athermalized” cylinder design (ID not effected by heat) can maintain good sealing of the piston at all cylinder temperatures.
A constant diameter cylinder has an inner liner made of a material with a higher coefficient of thermal expansion (CTE) and a lower Young's modulus than outer cylinder material. When heated, the liner tries to expand faster than the cylinder body but it is constrained from doing so by the smaller CTE of the cylinder. Since the outer cylinder expands less, the liner material is compressed and the inside diameter (ID) remains constant. Thus, a temperature gradient along the cylinder will not change the ID. The liner material (carbon filled polyimide, DuPont Vespel SP-21) was selected for self-lubrication and very low wear against the hard materials used for the piston. The Vespel liner wall thickness should be about 7% of the liner OD (inserted in a 440 stainless cylinder) to maintain constant ID over a wide temperature range. The liner is cooled before insertion into the outer cylinder.
The piston is fabricated from Invar alloy, which has a near-zero CTE. The piston is plated with electroless nickel (EN) hard coating to achieve low wear. Depending on the materials selected for the cylinder liner and piston plating, Teflon piston rings may – or may not – be required.
No Lubrication
Superheated steam (250-300 degrees C) provides little lubrication for a piston moving in a cylinder. By carefully choosing compatible materials for the cylinder liner and the piston coating, an engine requiring no lubrication can be achieved. When the piston has a very good fit to the cylinder (at all temperatures) and has a large contact area with the cylinder, hydrodynamic lubrication can be achieved when the piston is in motion. Under such conditions, wear is minimal – allowing the use of steam with no oil or other lubrication.
Test Results
A scale model of the engine was built with a cylinder ID of 18 mm, stroke of 36 mm, working pressure of about 30 bar (435 PSI), and speed of up to 6000 RPM. The model was coupled to a small generator and was tested with an electrically heated boiler and atmospheric pressure condenser. Efficiency was measured as the ratio of the electrical power produced by the generator, corrected for generator efficiency, divided by the boiler net heating power (about 1KW, which was the limit of the test boiler). While it is difficult to achieve high efficiencies in a small-scale model, the demonstration engine achieved an efficiency of about 10%. At 40 bar (580 PSI) pressure, in burst mode with steam stored in the boiler, the engine produced over 300W.
Scalability
The advanced uniflow steam engine can be scaled to larger sizes using modern materials and designs. The electromagnetic cutoff for the intake valve (no valve gear) is a major improvement. A constant diameter cylinder can be made from cast iron with a low-friction carbon-polymer liner (which is also a good insulator). An Invar piston with a diamond-like coating (DLC) may be able to achieve low wear and a good seal without piston rings. The front surface of the exhaust valve in the piston should be plasma coated with zirconia to insulate it from the inlet steam. With a constant diameter cylinder and a precise fit for the piston, a bulky crosshead mechanism may not be needed.
For a large stationary engine, other designs may work best, while still using electromagnetic cutoff for the intake valve. The cylinder could be machined with a tapered bore, to approximate constant diameter when heated at one end. Both the cylinder and piston may be plasma coated with zirconia. Piston rings of polymer/graphite or pure graphite can provide lubrication and a good seal. A crosshead will eliminate side forces of the piston on the cylinder, reducing wear. |